
In this model, the client has one point of contact, creating a seamless, integrated process from project conception to completion.
What is the Geis Design - Build - Develop Model?
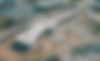
The Geis advantage
In today’s fast-evolving business landscape, companies are increasingly exploring innovative methods to build new facilities that not only support their operational needs but also streamline the construction process in order to bring new capacity on-line as soon as possible to maximize return on investment.
Leveraging the experience and capabilities of the Geis Design-Build-Develop model offers significant advantages. This approach integrates design, construction, and development into a single, cohesive solution, reducing risk, cost, and time, while ensuring a higher level of quality and efficiency.

The
Geis Advantage
develop | design | build
In today’s fast-evolving business landscape, companies are increasingly exploring innovative methods to build new facilities that not only support their operational needs but also streamline the construction process in order to bring new capacity on-line as soon as possible to maximize return on investment.
Leveraging the experience and capabilities of the Geis Design-Build-Develop model offers significant advantages. This approach integrates design, construction, and development into a single, cohesive solution, reducing risk, cost, and time, while ensuring a higher level of quality and efficiency.

Develop
Geis is the Developer and handles site acquisition, project financing, permits, and all other aspects related to real estate, using the integrated A/E and Construction staff as resources for due diligence. Geis’ Capital solutions include but are not limited to; Traditional Build-To-Suit transactions, Lease-To Own, Developer For Hire, Equipment & Premises financing on owner-occupiers behalf.

Design
Geis is the Architect and Engineer. The A/E staff are Geis staff and they create a custom facility design that meets the company's operational needs. They are solely dedicated to the project and are not juggling multiple assignments as general architectural firms must do. Geis staff are focused on the project.

Build
Geis is the builder and is solely responsible for managing the construction of the facility. Geis owns the risk of schedule and budget.
key benefits to our model
1.
Streamlined Communication and Project Coordination
2.
Cost Predictability and Control
3.
Faster Time to Completion
4.
Reduced Risk
5.
Custom Design Tailored to Operational Needs
6.
Access to Financing Solutions
7.
One Stop for Post-Construction Services
1. Streamlined Communication & Project Coordination
One of the main challenges when undertaking a large construction project is coordinating between multiple contractors, vendors, and architects. Miscommunication or delays at any stage can have a ripple effect, causing the project to fall behind schedule or exceed the budget.
In the GDBD model, having a single entity handle design, construction, and development ensures that all aspects of the project are well-coordinated. There is no need for back-and-forth between separate entities, allowing for quicker decision-making and smoother communication. The project team can address any issues or changes in real-time, reducing the chances of project delays.
2. Cost predictability and control
One of the most significant risks for companies without experience in construction is cost overruns. Traditional methods often result in misaligned expectations regarding the final price tag, with unforeseen expenses arising during the construction process. The GDBD approach mitigates this risk.
Since the design, construction, and development phases are handled by Geis Companies, the manufacturing company benefits from:
-
Fixed-price contracts that provide clearer cost expectations, with a budget arrived at much sooner than traditional delivery models from the start.
-
Budget oversight by a single entity, which can prevent hidden costs from appearing later in the project.
-
Reduced change orders due to the cohesive planning and design process, everyone is on the same page from the start.
The integration of these roles makes it easier to adhere to budgets and prevent financial surprises.
3. Fast Time to completion
With traditional construction models, a manufacturing company may face delays as a result of miscommunication between the non-integrated project team of independent architect, contractor, and developer. Each phase must be completed before the next one begins, and any delays in the design process often lead to setbacks in the construction schedule.
By combining all three elements into one model, the GDBD process streamlines timelines:
-
Concurrent phases where design and construction phases can overlap, shortening the project duration. Often early work permits allow for site work and foundations to start months ahead of final interior construction.
-
Fewer delays due to better coordination among team members who work together from the outset.
-
Simplified permitting and approvals, since the developer handles all necessary zoning and governmental compliance.
4. reduced risk
Construction projects come with a variety of risks—financial, legal, and operational. The GDBD model helps mitigate these risks in several ways:
-
Single-point accountability means that the developer is responsible for all stages of the project. If delays or issues arise, the manufacturer is dealing with one party rather than multiple contractors.
-
Risk-sharing is borne by the integrated design-build-developer Geis Companies, ensuring that the manufacturer does not bear the brunt of unforeseen complications.
-
Built-in quality control across design, construction, and real estate ensures that the final product meets the manufacturer's needs and adheres to high-quality standards.
The GDBD model’s integrated approach reduces potential points of failure and minimizes the risk of costly mistakes.
5. Custom Design tailored to operational needs
Manufacturing companies require specialized facilities that support complex workflows, equipment, and safety standards. With a GDBD model, the manufacturer has a facility designed specifically for its operational needs. Key advantages include:
-
Operational efficiency: Designers and builders who understand the manufacturing process can create a space that maximizes workflow and productivity. Geis has design and built over 700 facilities, with over 250 consisting of specialized manufacturing for a variety of industries.
-
Flexibility: The GDBD model allows manufacturers to make changes to the design throughout the process without disrupting the entire project.
-
Specialized features: From energy-efficient systems to space optimized for specific equipment, the GDBD team can implement custom features that improve long-term operational performance.
6. Custom Design tailored to operational needs
For companies that have little experience with real estate or construction financing, the GDBD developer typically has established relationships with lenders and can help secure the necessary financing.
Developers often assist in navigating financial complexities, from construction loans to long-term financing options, ensuring the manufacturing company gets the best terms. Additionally, the developer’s involvement in the entire process allows for more accurate cost projections and the ability to secure funding with greater certainty.
7. one stop for post-construction services
Once the facility is completed, the GDBD model offers a single point of contact for ongoing maintenance and operational support. This simplifies warranty management and any adjustments required post-construction, such as renovations, facility upgrades, or repairs.
With the integrated approach of the GDBD model, post-construction services are generally more reliable and efficient.
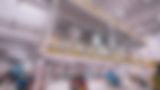
1. Streamlined Communication and Project Coordination
One of the main challenges when undertaking a large construction project is coordinating between multiple contractors, vendors, and architects. Miscommunication or delays at any stage can have a ripple effect, causing the project to fall behind schedule or exceed the budget.
In the GDBD model, having a single entity handle design, construction, and development ensures that all aspects of the project are well-coordinated. There is no need for back-and-forth between separate entities, allowing for quicker decision-making and smoother communication. The project team can address any issues or changes in real-time, reducing the chances of project delays.

2. Cost Predictability and Control
One of the most significant risks for companies without experience in construction is cost overruns. Traditional methods often result in misaligned expectations regarding the final price tag, with unforeseen expenses arising during the construction process. The GDBD approach mitigates this risk.
Since the design, construction, and development phases are handled by Geis Companies, the manufacturing company benefits from:
-
Fixed-price contracts that provide clearer cost expectations, with a budget arrived at much sooner than traditional delivery models from the start.
-
Budget oversight by a single entity, which can prevent hidden costs from appearing later in the project.
-
Reduced change orders due to the cohesive planning and design process, everyone is on the same page from the start.
The integration of these roles makes it easier to adhere to budgets and prevent financial surprises.

3. Faster Time to Completion
With traditional construction models, a manufacturing company may face delays as a result of miscommunication between the non-integrated project team of independent architect, contractor, and developer. Each phase must be completed before the next one begins, and any delays in the design process often lead to setbacks in the construction schedule.
By combining all three elements into one model, the GDBD process streamlines timelines:
-
Concurrent phases where design and construction phases can overlap, shortening the project duration. Often early work permits allow for site work and foundations to start months ahead of final interior construction.
-
Fewer delays due to better coordination among team members who work together from the outset.
-
Simplified permitting and approvals, since the developer handles all necessary zoning and governmental compliance.

4. Reduced Risk
Construction projects come with a variety of risks—financial, legal, and operational. The GDBD model helps mitigate these risks in several ways:
-
Single-point accountability means that the developer is responsible for all stages of the project. If delays or issues arise, the manufacturer is dealing with one party rather than multiple contractors.
-
Risk-sharing is borne by the integrated design-build-developer Geis Companies, ensuring that the manufacturer does not bear the brunt of unforeseen complications.
-
Built-in quality control across design, construction, and real estate ensures that the final product meets the manufacturer's needs and adheres to high-quality standards.
The GDBD model’s integrated approach reduces potential points of failure and minimizes the risk of costly mistakes.

5. Custom Design Tailored to Operational Needs
Manufacturing companies require specialized facilities that support complex workflows, equipment, and safety standards. With a GDBD model, the manufacturer has a facility designed specifically for its operational needs. Key advantages include:
-
Operational efficiency: Designers and builders who understand the manufacturing process can create a space that maximizes workflow and productivity. Geis has design and built over 700 facilities, with over 250 consisting of specialized manufacturing for a variety of industries.
-
Flexibility: The GDBD model allows manufacturers to make changes to the design throughout the process without disrupting the entire project.
-
Specialized features: From energy-efficient systems to space optimized for specific equipment, the GDBD team can implement custom features that improve long-term operational performance.

6. Access to Financing Solutions
For companies that have little experience with real estate or construction financing, the GDBD developer typically has established relationships with lenders and can help secure the necessary financing. Developers often assist in navigating financial complexities, from construction loans to long-term financing options, ensuring the manufacturing company gets the best terms. Additionally, the developer’s involvement in the entire process allows for more accurate cost projections and the ability to secure funding with greater certainty.

7. One Stop for Post-Construction Services
Once the facility is completed, the GDBD model offers a single point of contact for ongoing maintenance and operational support. This simplifies warranty management and any adjustments required post-construction, such as renovations, facility upgrades, or repairs. With the integrated approach of the GDBD model, post-construction services are generally more reliable and efficient.
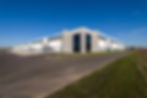.jpg)
Inquire Today!
